Sensors and actuators are at the heart of modern technology and are found everywhere in our everyday lives. Actuators are to technology what muscles or vocal chords are to us humans, for example, while sensors are like our sensory organs. They are the basis for the progress of our society, the way we live, work and interact with our environment. Electromechanical transducers convert electrical energy into mechanical energy and vice versa, making them sensors or actuators in practice. In our research, we develop new electromechanical transducers based on innovative ideas and explore the application and integration methods of sensors and actuators, including methods for encapsulation, power and data transmission.
Ferroelectrets
Ferroelectrets are piezoelectric polymers that feature noteworthy piezoelectric coefficients. The term ferroelectret is used since such films show a hysteresis effect upon charging and charge reversal. A synonymous term frequently used is piezoelectrets. These materials have been known for only about 20 years. They consist of a cellular polymer, often polypropylene (PP), containing gas voids of several μm in thickness and diameter. Such films are permanently charged by corona discharge or by contact electrification, resulting in barrier discharges in the voids. After charging, the films exhibit a reversible piezoelectric effect.
Energy Harvesting and Self-Sufficient Sensors
Combining factories with the Internet is the concept behind the fourth industrial revolution called as ’Industry 4.0’. However, industrial revolutions have so far been triggered not only by new data technologies, but also in combination with new energy sources. In fact, sensor networks that do not require batteries and transmit their data by wireless technologies are increasingly being used for monitoring of widely dispersed production and process engineering plants. In this context, energy harvesters are seen as the driving force behind this revolution as a way to provide these devices with the energy they need where electric power is not readily available.
3D-Printed Ultrasonic Ferroelectret Transducers
The operating principles of ultrasonic transducers are based on various physical fundamental principles such as the piezoelectric, magnetostrictive or electrostatic effect. Most transducers require an electrical DC bias for linearisation and increased sensibility in order to be used effectively. Piezoelectric transducers do not require such a DC bias, which simplifies the technical requirements and thus reduces costs, energy requirements and installation space. Ferroelectret transducers also have this advantage, as the electrical bias is not achieved via a DC voltage, but via a one-time induced electrical charge. Specific structures of polymers and air form cells that are first charged and then actuated to generate ultrasound. We want to combine this advantage with the benefits of the simple production of transducers using 3D printing and are thus developing our own ultrasonic transducers and ultrasonic transducer arrays with 3D printing processes. Our work starts with the basic development of new transducer concepts, the elaboration of concrete designs with the help of multiphysical simulation software and practical testing of possible manufacturing steps for practical production and the final characterisation of the transducers. Our research activities related to these transducers are part of an EU-wide research project on piezoelectric ultrasonic transducers and microphones called Listen2Future.
Force Measurement and Sensorintegration
Modern automation solutions, data-driven analytics, and Artificial Intelligence rely on high-quality sensor data. Research in the field of measurement and sensor technology addresses areas where commercial standard sensors are either not usable or require significant effort, from the measurement principle to encapsulation, and energy and data transmission.
The development of structurally integrated force and torque sensors using additive manufacturing is the focus of the AddKraft project. This manufacturing approach allows for highly individualized sensor designs, especially suited for complex structures in process monitoring, medical technology, and lightweight construction. Unlike conventional subtractive manufacturing of deformation bodies, additive manufacturing offers new geometric freedoms and enhanced integration possibilities.
Sensor-integrated Machine Elements
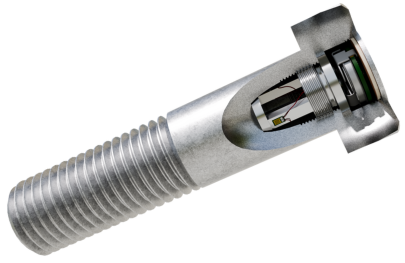
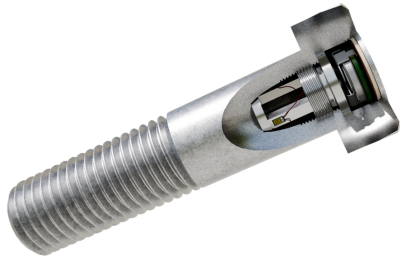
As part of the DFG Priority Program 2305 () , the integration of measurement technology into standardized machine elements is being researched. These standardized components are particularly suitable due to their widespread use and easy interchangeability. website
The SiSmaK subproject () focuses on the development of multi-axial force measurement in standardized bolts. Using finite element simulations, the mechanically relevant properties were quantified and compared with the necessary modifications for sensor integration in an optimization function ( project description) . This method ensures that the bolt continues to fulfill its purpose as a fastener while measuring axial and bending forces with an integrated sensor. read more
A miniaturized multi-component force sensor was developed (),for this purpose, capable of capturing the different measurement ranges of the various load components and featuring appropriate interfaces for mechanical integration into the bolt. publication
The prototype demonstrates the success of the method: Even under a large axial load, small transverse forces can be represented with just a finger press (). publication
3D-printed Force Sensors
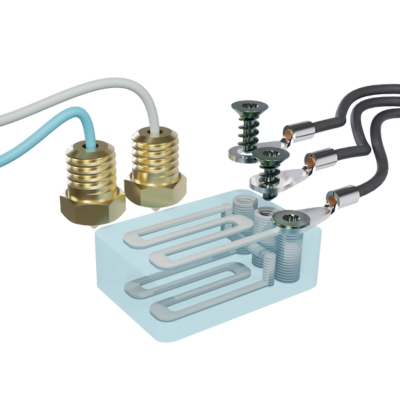
The availability of conductive materials for additive manufacturing opens new possibilities for the direct integration of sensor structures in FDM printing. In multimaterial 3D printers, conductive and insulating polymers are used together to integrate sensors directly into individual components, including compensation for disturbances such as temperature and full encapsulation. For example, affordable force sensors can be built for robotics and human-machine interfaces.
Read more about 3d printed force sensors in our publications on, using a printed force sensoror a printed sensors for experimentall stress analysis universal force sensor for versatile sensor integration
3D Printing Methods for Flexible Ferroelectret Sensors with Complex Structures
Flexible ferroelectret sensors offer numerous application possibilities thanks to the design freedom and material variety of 3D printing. However, manufacturing complex structures with well-defined air cavities poses a challenge, particularly for small dimensions and high surface quality requirements. By utilizing optimized printing processes, different materials can be processed, and sensor structures with high mechanical stability can be realized. These approaches enable the development of large-scale sensor arrays, which are particularly suitable for applications such as tactile interfaces.
For more information, see the related publication.