Starting from ultrasound images of an unborn child, to fingerprint recognition in smartphones, up to sonar systems for submarines – ultrasound is used in a wide variety of applications and in different media due to its mechanical wave properties. At the Measurement and Sensor Technology Group, we specialize in air-coupled ultrasound. Our research focuses on:
- Sonar systems for object detection and industrial imaging,
- waveguide technology for flexible array design,
- non-contact non-destructive testing of materials and
- high-velocity flow measurement,
- ultrasound-based force measurement,
- acoustic levitation for contactless manipulation of objects and
- gas-phase sono-photonics, exploring the interaction between acoustic waves and light in gaseous media,
- 3D-printed, biodegradable ferroelectric ultrasonic transducers.
In addition, our infrastructure, including a state-of-the-art anechoic chamber, enables precise measurements and experiments in a controlled environment.
Our work combines fundamental research with practical applications, opening up new possibilities in air-coupled ultrasound technology.
Contents
Hardware development
Ultrasound sensing
High-power ultrasound
Ferroelectret Ultrasonic Transducers
Research infrastructure
Ultrasonic Phased Arrays
A phased array is a group of multiple ultrasonic transducers. This enables the sound radiation to be steered in a specific direction when transmitting, as well as selective listening in a specific direction when receiving, without requiring the array to be moved mechanically. This technique is called beamforming and is based on phase-shifted excitation of the individual transducers. Transmit and receive beamforming is combined for pulse-echo detection in sonar systems to locate objects in three dimensions.
In general, waveguides are channels that carry a sound wave. This could be the sound we perceive through our auditory canal or our voice, which is carried through the throat. The geometry of the channel has a significant impact on the sound wave, for example when generating harmonics as we sing. In addition, waveguides provide a protective function by separating the sound-generating or sound-receiving surface from the free field.
This is exactly the approach we take to protect ultrasonic arrays, to optimize their acoustic properties, and to flexibly design array geometries. We rely on multiphysics simulations to investigate mode conversions, propagation time differences, and acoustic efficiency.
Acoustic waveguides – design and simulation
Reliability for challenging environments
Splashing cooling water, flying splinters and dense soot are not rare in industrial environments. When using arrays under these conditions, our waveguides provide protection for the ultrasonic transducers, however, clogging of the channel openings themselves may occur.
In order to ensure reliability, we investigate the suitability of protection systems, also used in smartphones or Bluetooth speakers, for example. The challenge is to protect the channels without severely impairing acoustic efficiency. Depending on the type of protection, various optimizations must be applied. For example, similar to a guitar string, the pretensioning of the membranes to the correct resonance frequency or the pore size of the hydrophobic textiles are crucial for acoustic efficiency.
Sonar systems and imaging
Advanced mobile robots must navigate safely in a variety of different environments. Smoke and dust, poor lighting conditions, as well as windows and reflective surfaces are major challenges for conventional monitoring sensors, such as cameras and lidars. Ultrasonic sonar systems reliably locate objects in three dimensions even under these conditions, thus, ensuring precise navigation and mapping.
Our research group investigates the capabilities and limitations of sonar systems regarding multiple optimization goals. A key factor is the viability in terms of real-time capability, computational effort, resolution, space and cost. For flexibility, we create our sonar systems from scratch – starting with array design, electronics, firmware and software development up to GPU-accelerated signal processing. In addition to the development and experimental characterization, we continue to evaluate the actual applications, for example by using a mobile robot.
Ultrasonic flow metering
Water vapor and natural gas are just two examples of gases that are passed on at high flow rates in industry. Ultrasonic flow measurement is particularly advantageous here because there is no pressure drop across the measuring device, thus saving energy. In cooperation with Prof. Pelz's Institute for Fluid System Technology, where a test stand with flow velocities of up to 107 m/s exist, we have tested ultrasonic flow measurement at high velocities. However, when one wants to measure such high flow velocities with ultrasound, the problem arises that the sound is blown away by the flow. Our solution to this is to compensate for sound drift with an ultrasonic phased array. We have built a research platform to study this and ensure accurate measurement even at high flow rates with ultrasound.
Non-Destructive Testing with Ultrasound
Non-destructive testing with ultrasound is a method for inspecting materials for irregularities or defects without damaging the test object. Ultrasonic waves are sent through the material to be tested. Air-coupled ultrasound has the advantage that no direct coupling to the material is required, which enables contactless testing. The recorded ultrasonic signal can be used to draw conclusions about possible defects or structural changes. This non-invasive testing method is used in various industries, from aerospace to the metalworking industry, to ensure the quality and integrity of components.
In this case, the air-coupled transmitter array excites a Lamb wave in the sheet steel by optimally triggering an ultrasonic pulse at the angle alpha. The Lamb wave is reflected by a defect, in this example a sawn cut-out in the steel sheet. The receiver array enables the reflected leaky Lamb wave to be detected, even if the direct air wave arrives at the same time.
Acoustic levitation for life sciences
Acoustic levitation is a fascinating technique that utilizes the forces generated by high-intensity sound waves to suspend objects in mid-air without physical contact. The underlying principle relies on the generation of standing wave fields, where acoustic pressure nodes and antinodes are formed. At the nodes, the acoustic radiation force can counteract gravitational forces, allowing objects to be levitated. This method is particularly advantageous because it does not rely on the material properties of the object, such as electrical conductivity or magnetism, making it a highly versatile and non-invasive tool for scientific research and industrial applications.
One of the most remarkable aspects of acoustic levitation is its ability to manipulate both solid and liquid matter, irrespective of size, shape, or physical state. This includes the levitation of biological entities, such as insects or small organisms, enabling studies of biological and chemical processes in a completely contactless environment. Unlike other levitation techniques, such as magnetic or electrostatic levitation, acoustic levitation is not limited by the need for specific material properties, thus broadening its range of potential applications. It has already proven useful in fields such as materials science, biophysics, and analytical chemistry, where contamination-free environments are essential.
The potential for acoustic levitation extends beyond simple suspension, as it also enables controlled manipulation and transport of objects. By modulating the acoustic field, levitated objects can be moved along predefined trajectories or positioned with high precision. This opens up possibilities for innovative applications, including micro-assembly, drug delivery, and the handling of hazardous materials in a safe, contactless manner. As research progresses, acoustic levitation is expected to significantly contribute to the advancement of technologies across diverse scientific and engineering disciplines.
Gas-phase sono-photonics
Conventional methods for controlling light are based on the interaction of light with solid materials, such as mirrors or glass fibers. This interaction poses challenges in two central aspects:
- The transmission properties of an optical system based on solid matter are limited in their bandwidth. This results in wavelength-dependent losses during transmission, which can ultimately lead to complete absorption.
- The solids can only cover their desired optical properties over a limited power spectrum. Laser applications with high optical peak powers in particular are coming up against those degradation limits.
The research field of gas-based sono-photonics is dedicated to overcoming these challenges. Here, a gas phase is modulated by means of intense ultrasound waves. The resulting periodic change in density in turn leads to a periodic modification of the optical refractive index. This makes it possible, for example, to create optical gratings for deflecting laser beams. Lasers deflected using ultrasound
Building on this successful demonstration, there are various research aspects at the junction between electrical engineering, ultrasound technology and optics. These include the implementation of new ultrasonic systems for the generation of intense, but also dynamic controllable sound fields, as well as their characterization using non-interfering optical methods. These systems form the basis for new sono-photonic elements, such as beam splitters, phase modulators and many more with a focus on previously unexplored optical parameter spaces.
Ferroelectret Ultrasonic Transducers
Air-coupled ultrasonic transducers are widely used in applications such as non-destructive testing, acoustic sonar systems, and biomedical imaging, where broad frequency response, adaptable designs, and sustainable materials are becoming increasingly important. Recent developments focus on biodegradable ferroelectret transducers made from polylactic acid (PLA), combining a PLA film as a vibrating plate, a 3D-printed backplate with defined air voids, and a holder for structural stability. These monolithic designs, produced via 3D printing, utilize trapped surface charges to provide electrical bias and mechanical pre-stress, enhancing their performance. The transducers demonstrate versatility and reliability, with their design enabling acoustic properties to be tuned for specific applications. The use of eco-friendly PLA materials further supports sustainable innovation, making these transducers particularly suitable for imaging and biomedical uses.
For more information, see the related und publication (monlithic design) publication (pre-stressed design).
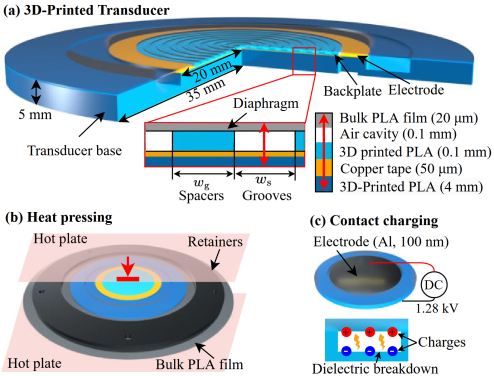
Schematic of a 3D-printed ultrasonic transducer based on ferroelectrets, featuring a monolithic structure with thermally fused PLA film and air cavities. High voltage induces quasi-static charges, forming the ferroelectret.
Controlled test environment – anechoic chamber
In order to conduct acoustic characterizations under controlled environmental conditions, we maintain a fully insulated, anechoic chamber. This room is decoupled from the building's foundation, so that mechanical vibrations from the outside do not interfere with our measurements. We use a goniometer setup consisting of two rotational axes and one linear axis to freely position calibrated measurement microphones, senders or targets. This allows us to automatically characterize ultrasonic transmitters, receivers, arrays and sonar systems in three dimensions.