Sensoren und Aktoren sind das Herzstück moderner Technologie und sind überall in unserem Alltag zu finden. Aktoren sind für Technik das, was für uns Menschen beispielsweise Muskeln oder Stimmbänder sind, während Sensoren unseren Sinnesorganen entsprechen. Sie sind die Grundlage für die Weiterentwicklung unserer Gesellschaft, die Art und Weise, wie wir leben, arbeiten und mit unserer Umwelt interagieren. Elektromechanische Wandler konvertieren elektrische Energie in mechanische Energie und umgekehrt, was sie in der Praxis zu Sensoren oder Aktoren macht. In unserer Forschung entwickeln wir auf der Basis innovativer Ideen neue elektromechanische Wandler, untersuchen den Einsatz und Integrationsmethoden von Sensoren und Aktoren, inklusive Methoden zur Verkapselung, Energie- und Datenübertragung.
Ferroelektrete
Ferroelektrete sind piezoelektrische Polymere, die bemerkenswerte piezoelektrische Koeffizienten aufweisen. Der Begriff Ferroelektret wird verwendet, da solche Folien bei Aufladung und Ladungsumkehr einen Hystereseeffekt zeigen. Ein häufig synonym verwendeter Begriff ist Piezoelektrete. Diese Materialien sind erst seit etwa 20 Jahren bekannt. Sie bestehen aus einem zelligen Polymer, oft Polypropylen (PP), das Gasporen von einigen μm Dicke und Durchmesser enthält. Solche Folien werden durch Koronaentladung oder durch Kontaktelektrisierung permanent aufgeladen, wodurch es in den Hohlräumen zu Barriereentladungen kommt. Nach der Aufladung weisen die Folien einen reversiblen piezoelektrischen Effekt auf.
Energy Harvesting und autarke Sensoren
Sensornetzwerke, die keine Batterien brauchen und ihre Daten durch drahtlose Technologien übertragen, werden immer häufiger zur Überwachung von weit verstreuten Produktions- und verfahrenstechnischen Anlagen gewünscht. In diesem Zusammenhang werden „Energy-Harvester“ als die treibende Kraft hinter die Industrie 4.0 gesehen. Diese sichern die Versorgung der Elektrogeräte mit der benötigten Energie, da wo die elektrische Energie nicht ohne Weiteres zur Verfügung gestellt werden kann.
3D-gedruckte Ferroelektret Ultraschallwandler
Die Funktionsweisen von Ultraschallwandlern basieren auf verschiedenen physikalischen Grundprinzipien wie dem piezoelektrischen, magnetostriktiven oder elektrostatischen Effekt von schwingenden Kondensatoren. Die meisten Wandler benötigen für eine Effektive Nutzung einen elektrischen DC Bias zur Linearisierung und Erhöhung der Empfindlichkeit. Piezoelektrische Wandler kommen ohne einen solchen DC Bias aus, was die technische Anforderungen vereinfacht und damit Kosten, Energiebedarf und Bauraum reduziert. Ferroelektretwandler, haben diesen Vorteil auch, da die elektrische Vorspannung nicht über eine DC-Spannung, sondern über eine einmalig aufgeprägte elektrische Ladung erreicht wird. Spezielle Strukturen von Polymeren und Luft bilden so Zellen, die zunächst aufgeladen und dann angesteuert werden, um Ultraschall zu erzeugen. Wir möchten diesen Nutzen mit den Vorteilen der einfachen Herstellung von Wandlern mit 3D-Druck verknüpfen und entwickeln so eigene Ultraschallwandler und Ultraschallwandlerarrays mit 3D-Druckverfahren. Unsere Arbeit beginnt bei der Grundlegenden entwickeln neuer Wandlerkonzepte, Ausarbeitung konkreter Designs mit Hilfe von multiphysikalischen Simulationsprogrammen und praktischen Erprobung möglicher Herstellungsschritte für die praktischen Herstellung und der abschließenden Charakterisierung der Wandler. Unsere Forschungsaktivitäten im Zusammenhang dieser Wandlern sind Teil eines EU-weiten Forschungsprojekts zu piezoelektrischen Ultraschallwandlern und Mikrofonen namens Listen2Future.
Kraftmessung und Sensorintegration
Moderne Automatisierungslösungen, datenbasierte Analysen und Künstliche Intelligenz sind auf qualitativ hochwertige Sensordaten angewiesen. Die Forschungsarbeiten am Fachgebiet Mess- und Sensortechnik adressieren dabei insbesondere Bereiche, bei denen kommerzielle Standardsensoren nicht oder nur mit erheblichem Aufwand einsetzbar sind vom Messprinzip über die Verkapselung bis zur Energie- und Datenübertragung.
Strukturintegration in der additiven Fertigung
Die Entwicklung strukturintegrierter Kraft- und Drehmomentsensoren mittels additiver Fertigung steht im Fokus des Projekts AddKraft. Dieser Fertigungsansatz ermöglicht eine hochgradig individualisierte Sensorgestaltung, die sich besonders für komplexe Strukturen in der Prozessüberwachung, Medizintechnik und im Leichtbau eignet. Im Gegensatz zur konventionellen spanenden Fertigung von Verformungskörpern bietet die additive Fertigung neue geometrische Freiheitsgrade und verbesserte Integrationsmöglichkeiten.
Sensorintegrierende Maschinenelemente
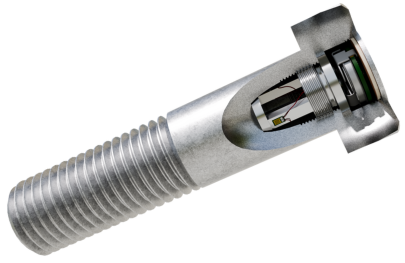
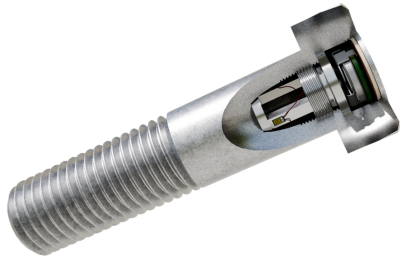
Im Rahmen des DFG-Schwerpunktprogramms 2305 () wird die Integration von Messtechnik in standardisierte Maschinenelemente erforscht. Diese standardisierten Komponenten sind besonders durch ihre weite Verbreitung und einfache Austauschbarkeit geeignet. Website des Schwerpunktprogramms
Das Teilprojekt SiSmaK () konzentriert sich dabei auf die Entwicklung mehraxialer Kraftmessung in genormten Schrauben. Mittels Finite-Elemente-Simulationen wurden die mechanisch relevanten Eigenschaften quantifiziert und mit den notwendigen Änderungen für eine Sensorintegration in einer Optimierungsfunktion gegenübergestellt. Diese Methode ( Link zum Projekt) stellt sicher, dass die Schraube weiterhin ihren Zweck als Verbindungselement erfüllt und dabei die wirkenden Axial- und Biegelasten mit einem integrierten Sensor messen kann. Link zur Veröffentlichung
Dazu wurde ein miniaturisierter Mehrkomponenten Kraftsensor entwickelt (), der die unterschiedlichen Messbereiche der unterschiedlichen Lastkomponenten aufnehmen kann und entsprechende Schnittstellen zur mechanischen Integration in die Schraube aufweist. Link zur Veröffentlichung
Der Prototyp demonstriert den Erfolg der Methode: Selbst bei einer großen axialen Belastung können geringe Querkräfte schon durch Druck mit dem Finger dargestellt werden (). Link zur Veröffentlichung
3D-gedruckte Sensorstrukturen
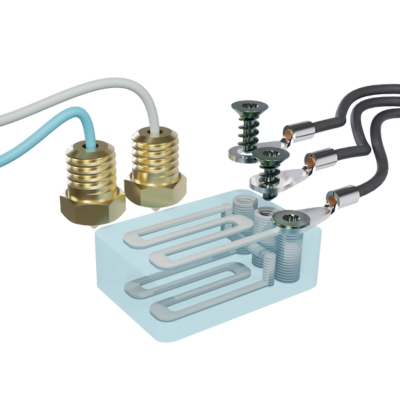
Die Verfügbarkeit leitfähiger Materialien für additive Fertigungsverfahren eröffnet neue Möglichkeiten zur direkten Integration von Sensorstrukturen im Bereich des FDM-Drucks. Im Multimaterial Drucker werden leitfähige und isolierende Polymere gemeinsam genutzt, um direkt in individuellen Komponenten Sensoren zu integrieren, inklusive Kompensation von Störgrößen wie der Temperatur und vollständiger Verkapselung. So können zum Beispiel günstige Kraftsensoren für die Robotik und Mensch-Maschine Schnittstelle aufgebaut werden.
Lesen Sie mehr zum Thema in unseren Veröffentlichungen über den , die Nutzung Aufbau eines gedruckten Kraftsensorsoder der vollständigen gedruckter Dehnungsmesstreifen zur Stresanalyse universellen Integration in generischen Druckteilen.
3D-Druckverfahren für flexible Ferrolektretsensoren mit komplexen Strukturen
Flexible Ferrolektretsensoren bieten dank der Designfreiheit und Materialvielfalt des 3D-Drucks zahlreiche Anwendungsmöglichkeiten. Die Herstellung komplexer Strukturen mit definierten Luftkammern stellt jedoch eine Herausforderung dar, insbesondere bei kleinen Dimensionen und hohen Anforderungen an die Oberflächenqualität. Durch optimierte Druckprozesse können unterschiedliche Materialien verarbeitet und Sensorstrukturen mit hoher mechanischer Stabilität realisiert werden. Diese Ansätze ermöglichen die Entwicklung großflächiger Sensorarrays, die sich besonders für Anwendungen wie taktile Schnittstellen eignen.
Weitere Informationen in der Veröffentlichung.